自動車のプラスチック採用は内側から外側へ
自動車部品にプラスチックを採用する流れは、当初はインスツルメントパネル(インパネ)やダッシュボード、ドアポケットなど自動車の内側から始まりました。それが次第にフロントグリル、ドアミラースペース、リアランプカバー、フロントスペーサー、リアサポートなど自動車の外側に移行し、今ではリアサスペンションバッファー、燃料タンク、ステアリングカラムトリム、ラジエータータンクのインタークーラーにも用いられています。プラスチックはいかに材料特性を有効に活用するかが問われています。
ポリエチレン系プラスチック
たとえばポリエチレン系プラスチックは、元素構造が「炭素-炭素」結合からなり、製品特性としてはやや柔らかいプラスチックです。化学的には安定しており、酸やアルカリに侵されず、加水分解もされません。油やガソリンなど有機薬品にも強いという性質を持っています。ただ耐候性は高くないため直射日光(特に紫外線)にさらされるとすぐに劣化してしまいます。
そのためにポリエチレン類は、自動車内部の燃料タンク、ブレーキオイルタンクなど容器類に採用されています。金属製の燃料タンクは非常に重くなりますが、これがポリエチレン製になって軽量化が一気に進みました。またデザインの自由度や耐腐食性、衝突時の安全性にも優れ、何よりもコストダウンが進みます。燃料タンクは最も普及したプラスチック部品でもあります。
ポリプロピレン系ブラスチック
ポリプロピレン系ブラスチックは化学構造の違いから種類が多岐にわたります。耐衝撃性や透明性に優れており、フィルム類や合成ゴムへのブレンド材に用いられます。
今では自動車のプラスチック部品の中でも、ポリプロピレン系の部品が過半数以上の比率を占めており、最も多用されているプラスチック部品です。ここまで普及した理由として、広い温度範囲にわたって機械的な強度が得られること、表面特性を含めた加工性が高いこと、軽量でリサイクルが容易なこと、価格が安いこと、などの利点があるためです。
ポリプロピレン系部品の弱点は耐候性で、低温における耐衝撃性にも難があります。これには表面塗装をほどこすことで耐候性はカバーでき、低温での耐衝撃性にはゴム成分をブレンドする技術が発達してきたことで補います。現状では-30℃の低温条件での衝突にも耐えうるポリプロピレン系部品も開発されています。
ポリプロピレン系部品の進化を示す事例のひとつとして、バンパーへの採用があります。
バンパーに求める役割が変化しています。初期の頃は衝突に際して、車体の保護と運転手や乗客の安全を守ることがバンパ-の目的でした。それが近年は歩行者との衝突の際に、歩行者へのダメージを最小限にするような設計が求められています。
それによってバンパーシステムに採用される材料も、初期のころの鉄板から近年はデザイン性に優れたポリウレタンやポリプロピレン系コンパウンド(複合物、配合剤)が使用されるようになりました。今では乗用車など大量生産される車種のバンパーは、ほとんどがポリプロピレン系コンパウンドなどの熱可塑性プラスチックで占められています(熱可塑性。加熱して軟化させて成形し、その後に冷却すれば固化する性質を有する樹脂)。
何よりも低コストで成形がしやすく、機械的な強さもあり、曲げ強さでは鋼材並みの強度が得られる点が高く評価されています。
ポリスチレン系プラスチック
プラスチック部品の代表格としてもうひとつ、ポリスチレン系プラスチックがあります。これにはスチレンだけから作られるポリスチレン・ホモポリマーと、ABS樹脂のようなスチレンに他のモノマーを加えて作られたターポリマー(3元共重合体)など、非常に多くの種類のプラスチックがあります。
一般にポリスチレン系プラスチックは、耐熱性はそれほど高くありませんが、熱安定性がよく、酸やアルカリにも侵されず、価格が安く加水分解もされないため、日用品から工業用品まで幅広く使用されています。
耐熱性に難点があるため、ポリスチレン系プラスチックは自動車部品としてはあまり採用されず、むしろ耐薬品性、高い電気特性、寸法精度の高さ、加工性のよさから家電製品に多く用いられてきました。これからは電気自動車の普及拡大に伴って、自動車業界でもポリスチレン系プラスチック性の部品の採用が今まで以上に増えることになると考えられます。
すでに現状でも多く採用されているのがABS樹脂です。これはアクリロニトリルとブタジエン、スチレンの3種類のモノマー(重合を行う際の基質。単量体。モノマーが多数結合した高分子がポリマー)から作られたターポリマーです。
ポリスチレンの持つ剛性、電気特性、耐熱劣化性、表面特性を有しつつ、さらに耐衝撃性、耐熱性、耐溶剤性も備えた非常にバランスの良いプラスチック部品です。ただしやはり耐候性には難があります。
ABS樹脂は射出成型に最も適したプラスチックとされており、大量生産による部品の製造にも適しています。今では運転手の安全を守るシートをはじめ、センターコンソール、グローブボックスなど広い範囲で部品として用いられています。
「車体の軽量化」は最大のテーマのひとつ
地球温暖化の弊害は一刻の猶予もならない状況を迎えています。環境規制の一段の強化は避けられません。自動車業界が生き延びるには、世界的に高まる電気自動車や燃料電池車への移行を急ぐしかありません。そこでは「車体の軽量化」は最大のテーマのひとつであり、プラスチック材料のさらなる活用こそ人類に求められている新たな技術革新への挑戦なのです。
大手化学メーカーの中でも、自動車向け高機能プラスチックに強い、三井化学(4183)、信越化学工業(4063)、東ソー(4042)、リケンテクノス(4220)、日精樹脂工業(6293)、信越ポリマー(7970)に注目しています。
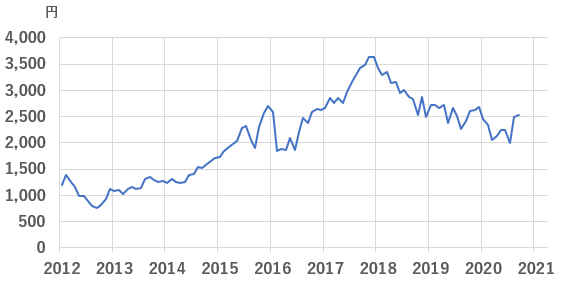
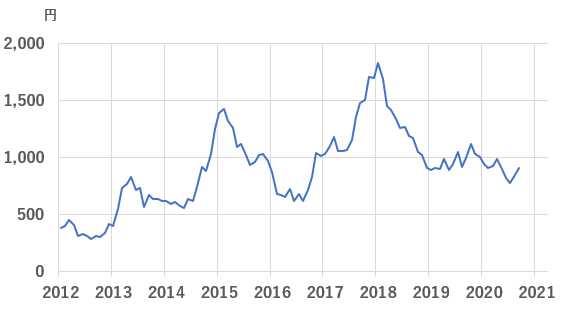